This post is also available in: polski (Polish)
Modern production processes are becoming increasingly complicated, at the same time customers demand higher quality products at the lowest possible price. This situation increases the importance of process optimization. Due to the fact that technologies, products and requirements change faster and faster, technologists have less and less time to learn the process and optimize it solely on the basis of their own experience. On the other hand, very often the processes are automated and measured in details what provides us with a large amount of data describing them accurately.
In such a situation, the opportunity to support decisions with the results of modern data analysis cannot be simply rejected. Data analysis may be used to optimize processes in various ways and be related to many aspects of process management. We are able to detect disturbances in the process, find causes of quality problems, select optimal settings for a process, compare various procedures of manufacturing and many others.
It is worth noting that processes, and thus their optimization, are related to the involvement of many people with different tasks, various experience and permissions. Therefore, a data analysis tool should allow multi-person cooperation, ensure access control, and easy use of data and results. The research project assumes the creation of two measurement platforms: a set of multiphase flow system and a mini production line. In the first case, the set will reflect the flow of liquid and air, which is especially important in all types of chemical reactors where air is used to mix the substances.
In the second case, the set will reflect the work of production line on which the items(products) move. These items will be identified on the basis of RFID tags (Radio-Frequency IDentification), as well as with the help of image detection techniques. This set, also using biometric readers, will ensure access control to operate the device.
Figure 1. Scheme of the construction of a measurement probe in electrical capacitance tomography..
The main problem in the described imaging technique is the measurement of capacitance of the fF order. Contemporary designs of tomographs carry out capacity measurement using the “charge-discharge” method. It consists in cyclic charging and discharging of the capacitor with simultaneous recording charging current, which is directly proportional to the measured capacity.
Capacitance tomography is widely used in the energy and petrochemical industry. It is mainly used in quantitative and qualitative control of materials transported in pipelines. Its main advantages include high speed of creating tomographic images, the ease of assembly of measurement system, as well as the low level of complexity.
Alternatively, techniques based on X-rays or ultrasound waves are used, however, these types of solutions are costly and more problematic to implement.
The advance of capacitance tomography is closely related to the development of algorithms and image reconstruction methods. Despite many successes, the application possibilities of this method are not fully used. The reason for this is the lack of uniform standards which would allow for the full potential of this imaging technique to be used.
Hardware concept of a set for multiphase flow testing
The measurement platform is based on a set for testing multiphase flows. The scheme of the set is presented in the figure below (fig. 2).
Electrical capacitance tomography – technology description
Electrical capacitance tomography (ECT) is an imaging technique invented in the 1980s. It was created to determine the distribution of materials (fluids) inside closed spaces on the basis of measurements of the mutual capacitance of surface electrodes surrounding the tested object. Typical measuring systems use 8 to 16 electrodes symmetrically placed around the cylindrical container (tube), as shown in the figure below.
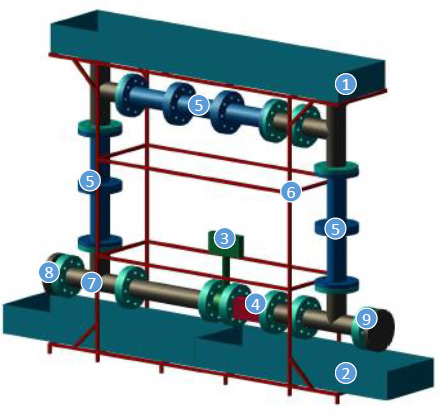
The design of the set enables testing of vertical, as well as horizontal flows. The use of control elements such as: throttle, circulating pump or (air) solenoid valves, enable precise and repeatable reproduction of the measurement conditions. Additionally, this configuration allows for studying countercurrent flows, very important from the point of view of applications in real industrial installations.
The use of transparent elements allows for simultaneous flow control with image detection methods. At the same time, this set enables ECT correlation with the use of two sets of measuring electrodes.
The presented measuring system is used not only to study different types of multiphase flows, but most of all to develop algorithms used in electrical capacitance tomography.
One of the main goals of these studies is creating a uniform system, which will ensure the optimization and control of the production process. The figure below (fig.2) shows the model of the system, which consists of the optical detection system based on industrial IP cameras and a capacitance tomography system.
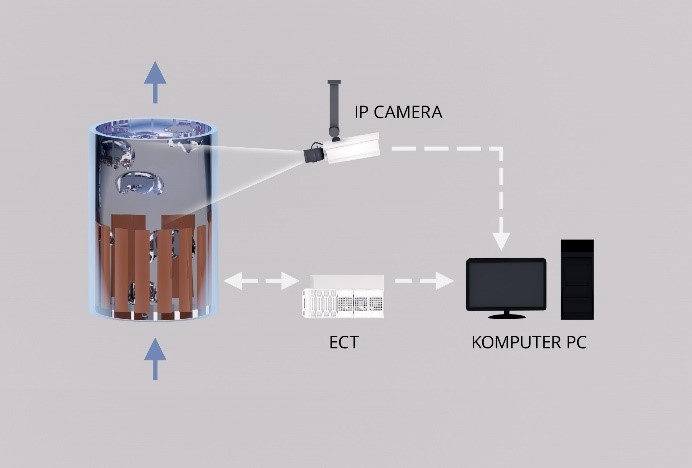
Fig. 3 Schematic model of the measuring system of the set for flows testing
Hardware concept of a production line set
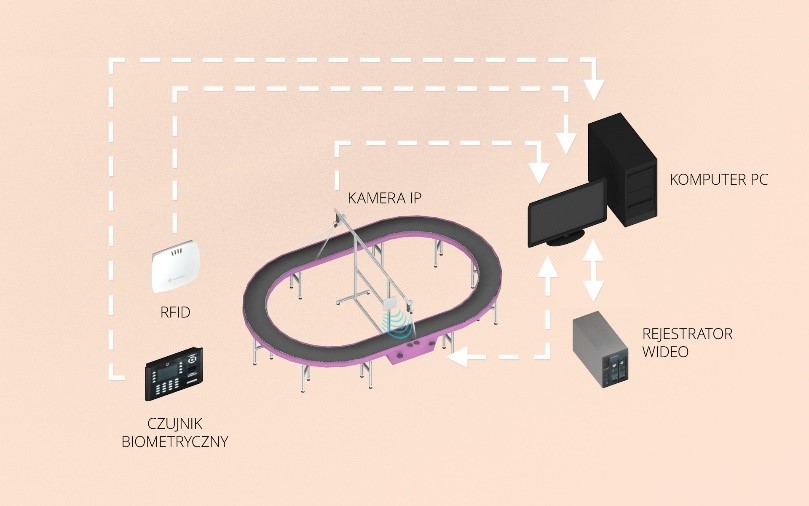
Fig. 4. Scheme of the measuring system of the production line
The measuring system includes IP cameras, RFID reader, biometric readers and the image recording system (DVR). Access control to the production line control panel is ensured by the system of biometric readers, which on the basis of the fingerprint of the “employee” will authorize the user to introduce changes, for instance in the speed of the belt. The optical detection system, similarly to previous solutions, is based on IP cameras.
The video image from cameras will be analyzed in real time, recognizing moving objects on the basis of their characteristic features e.g. shape, size, color. At the same time, the image will be saved on the disk array. Additional identification of objects will be carried out by means of programmable RFID tags placed on their surface.
Such a system will not only ensure a precise micro-scale representation of a production plant, but also constitute the basis for the development of fast algorithms.
If you want to know more, please contact us. We will be happy to answer all your questions and find the perfect solution for your business.